塑料垃圾桶的注塑成型工艺具体是如何操作的
垃圾桶的制作工艺因材质不同而有所差异,以下是几种常见材质的垃圾桶制作工艺:
一、塑料垃圾桶
注塑成型:将塑料颗粒加热熔融后注入模具,冷却后形成桶体结构。模具设计与制作:依据产品设计图纸制作高精度模具,确保生产效率和一致性。表面处理:进行静电喷涂、UV涂层等处理,增强美观性和耐用性。
二、金属垃圾桶
冲压与焊接:通过冲压、切割、焊接等工艺完成桶体成型。表面处理:进行防锈处理,如镀锌或喷漆,以提高耐腐蚀性能。
三、木质垃圾桶
裁剪与打磨:对木材进行裁剪、打磨,确保形状和表面光滑。防腐处理:进行防腐处理,以延长使用寿命。
塑料垃圾桶的注塑成型工艺主要操作步骤如下:
一、原料准备
选材
根据垃圾桶的性能要求(如强度、韧性、耐候性等)选择合适的塑料原料,常见的有聚乙烯(PE)、聚丙烯(PP)等。
干燥处理
将塑料原料进行干燥,去除其中的水分。因为水分会影响注塑产品的质量,如产生气泡等缺陷。干燥的温度和时间根据原料的种类而定,例如PP原料一般干燥温度为80 - 90℃,干燥时间为2 - 4小时。
二、注塑机参数设定
温度设定
料筒温度:根据塑料原料的熔点设定料筒各段温度。对于PE或PP原料,料筒前段温度一般设定在180 - 220℃,中段温度略低,后段温度较低。喷嘴温度:喷嘴温度通常比料筒前段温度低10 - 20℃,以确保塑料熔体在喷嘴处不会过早固化。
压力设定
注射压力:根据垃圾桶的大小、形状和塑料原料的流动性设定注射压力。一般小型垃圾桶注射压力在80 - 120MPa,大型垃圾桶可能需要150 - 200MPa。保压压力:保压压力通常为注射压力的50% - 80%,用于补充塑料熔体在冷却过程中的收缩,防止垃圾桶出现缩孔等缺陷。
时间设定
注射时间:根据垃圾桶的壁厚等因素确定,一般为2 - 5秒。保压时间:保压时间与垃圾桶的壁厚有关,壁厚越大,保压时间越长,通常在10 - 30秒。冷却时间:冷却时间根据垃圾桶的尺寸和塑料的冷却速度而定,一般为20 - 60秒。
三、注塑成型过程
加料
将干燥好的塑料原料加入注塑机的料斗中,原料会自动进入料筒。
塑化
料筒中的螺杆旋转,将塑料原料向前输送并在高温下塑化,使塑料成为均匀的熔体。
注射
融化的塑料熔体在注射压力的作用下,通过喷嘴注入到预先设计好的模具型腔中,填充整个型腔以形成垃圾桶的形状。
保压
注射完成后,螺杆继续保持一定的压力(保压压力)一段时间,以补偿塑料熔体冷却收缩造成的体积减小。
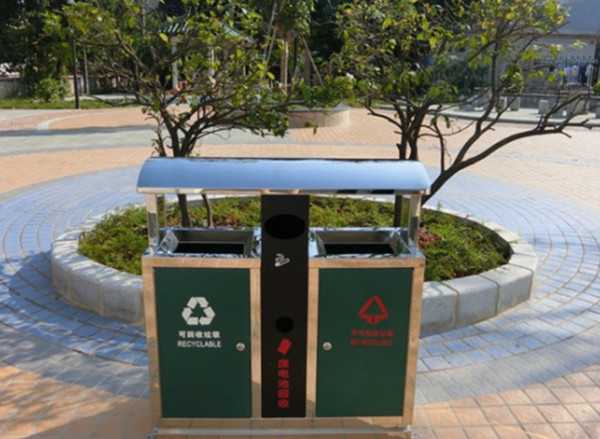
冷却
在保压结束后,模具的冷却系统开始工作,使垃圾桶在模具内冷却固化到足够的强度,以便脱模。
脱模
当垃圾桶冷却到一定程度后,打开模具,通过顶出机构将垃圾桶从模具中顶出。
四、后处理
修整
脱模后的垃圾桶可能会有一些飞边、浇口痕迹等多余的部分,需要使用刀具等工具进行修整去除。
质量检测
对注塑成型的垃圾桶进行质量检测,包括外观检查(如表面是否有缺陷、颜色是否均匀等)、尺寸检测(是否符合设计要求)等,不合格的产品会被剔除。